Block manufacturers in the Ashanti Region have expressed dissatisfaction with the quality of raw materials on the market.
They observed that a reduction in the quality and size of essential materials such as cement and iron rods is compromising the standard of their block production, ultimately affecting their profit gains.
Players in the construction industry have urged the Ghana Standards Authority to strengthen its surveillance of building products on the market.
Antiquated buildings erected amongst contemporary settlements have proven to stand the test of time, which according to experts, owe mainly to the quality of raw materials employed in their construction.
But block manufacturers argue recent metrology and quality of raw materials for building works are failing to meet the standard.
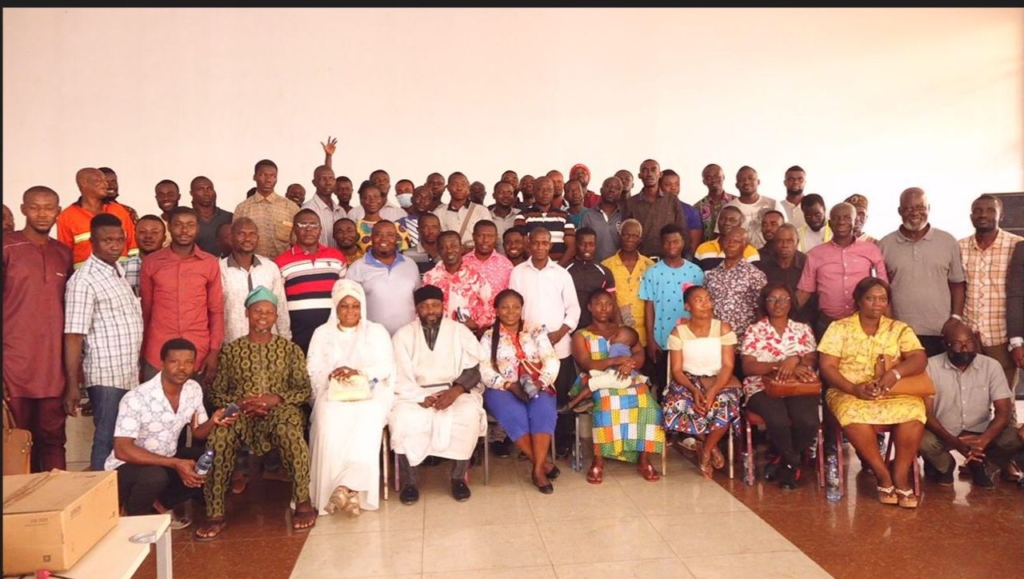
Manager for Akadire Blocks Factory, Ayingura Awene was worried about the emerging challenge.
“The sand, the quarry products that we procure, cement and irons have had all their standards compromised. Now, there is influx of cement which is good for the economy. But one of the challenges we’ve identified off late is that the weight of the cement is not good. It affects the design, especially for those of us who work with volumes. Because they may think one bag of cement is 50kg, perhaps that’s the dimension so they will be adding on other materials to get the products. So they just add up without taking the real measurement. At the end of the day, there could be some form of deficiency in their products,” he said.
In 2018, the government in collaboration with the Ghana Standards Authority established the National Building Code to ensure the safety of all public, residential and industrial buildings across the country.
The policy aims at streamlining actors in the Ghanaian construction industry with a common standard for public safety and protection, structural efficiency and environmental integrity.
In response to the concerns raised at a sensitization workshop, Acting Director of the Middle Belt of the Ghana Standards Authority, Samuel Kofi Frimpong, assured of stringent measures to rid the market of the substandard products.
“Our people will quickly go on the ground to conduct the checks. We will also contact the manufacturers to facilitate the location of these producers so we test their products and make sure it meets the standard. If it doesn’t, there will be penalties and even shutting down of factories to ensure there is sanity in the industry,” he assured.
Meanwhile, the industry players are calling for a review of policies guiding block certification.
They argue the exorbitant cost for the certification does not commensurate with the present market environment and may have tolling effects on their business.
“The law that was passed there wasn’t any proper consultations. Whenever we query them they tell us the consulting they did was 20 years ago. As of that time, the quality of the materials used for the production was different and so was the environment. They didn’t conduct any market analysis. They should have consulted us before passing the law,” one of the manufacturers emphasized.